Chemical Reaction Engineering Blog Posts

Better Brewing: Modeling Beer Fermentation
What’s brewing? Explore how modeling and simulation can be used to study the beer fermentation process, identifying ways to optimize its efficiency and serve up a better-tasting glass of suds.

Thermochemical Conversion of Biomass Through Pyrolysis of Wood
Pyrolysis converts biomass into products such as solid charcoal, which can further be refined into hydrogen. Here, read about modeling pyrolysis with the help of parameter estimation.
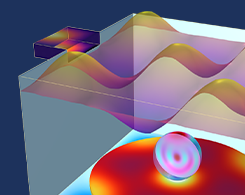
The Use of COMSOL Multiphysics® in the Food Industry
Food for thought: Explore how previously failed products and the use of multiphysics simulation inspire innovation in the food industry.
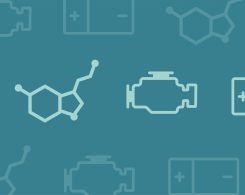
A Practical Sedimentation App for Toxicology Analysis
Sedimentation is widely used in toxicology, biochemistry, and biomedicine. You can study how gravity affects this physical phenomenon with simulation.
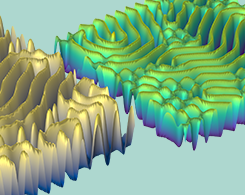
Visualizing the Emergence of Turing Patterns with Simulation
Turing patterns are often found in nature. The conditions behind the emergence of these patterns can be studied with chemical modeling.
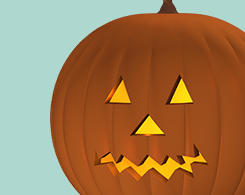
Extracting DNA: From Pumpkins to Mammoths
Here, we go over how to recover DNA from a pumpkin using a simple experiment, as well as how scientists made a recent breakthrough in DNA extraction research.
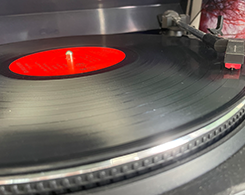
The History and Science Behind Vinyl Records
As vinyl records explode in popularity, we take a look back at the history of records, as well as the interesting science behind how they are produced — and how they play music.
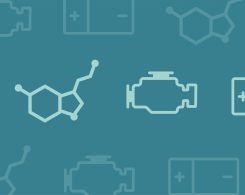
How to Model Metabolic Reaction Networks with COMSOL®
Certain ice creams, puddings, and candies have an extremely vivid yellow color that comes from vitamin B2. The manufacturing of this supplement is one example of a metabolic reaction network…