Design of a Self-Recharging Untethered Mobile Inspection Tool inside a Pipeline
Pipeline inspection tools present some limitations related to power supply which require recharging after each operation. Using batteries or tethered tools make the duration to inspect any pipeline very limited and time consuming. This paper aims at designing a spherical self-recharging untethered mobile ball flowing inside a given pipeline using the COMSOL Multiphysics® software. The ball will be equipped with the necessary sensors to be able to detect any leaks through acoustic waves, pressure differential, and other necessary sensors and then send a signal to the supervisors once a leak was detected. In addition, the ball can detect any potential leak locations by measuring the pipeline wall thickness; thereby, alerting pipeline engineers of any expected damages. The ball will be fully autonomous and will not need any change of battery using built-in blades, designed using the COMSOL® software, and installed inside the spherical ball. The blades will use the force of the flow in order to rotate and generate a magnetic field that will induce a current. Thus, as long as the ball is propelled inside the pipeline by the fluid motion, the ball will be self-recharged. Also, the Computational Fluid Dynamics (CFD) Module of the COMSOL® software was used to simulate the fluid flow around the blades and the associated energy to be used for charging the battery. The battery life can be determined from the obtained data. The results from the velocity and pressure propagation will be used to optimize the design of the blades as well as the outer shell of the ball. In addition, the Acoustics Module of the COMSOL Multiphysics® software will be used to optimize the location of the sensors connected the control system inside the mobile ball, by analyzing the sound propagation from a possible leak. The control system will analyze the data from the multiple sensors and send an immediate signal to the supervisors describing the leak size and location once any sudden change of the fluid flow velocity, pressure or sound level is detected. Finally, the COMSOL® software will be used to conduct a sensitivity analysis where different fluid types, leak sizes and pipeline diameters are compared to find the optimal design of the mobile ball and the optimal blades shape. The optimal design is intended to generate enough power to recharge the batteries using the fluid flow. By having an autonomous power supply, this inspection tool will have a high accuracy and efficiency. The data will always be in real time and continuous. Therefore, the need to take out the ball from the pipeline and change the batteries is no longer required and no waste of time will be present.
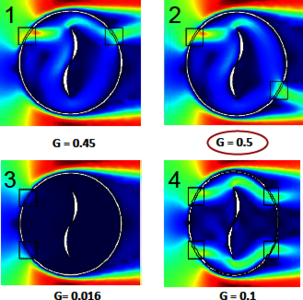
Download
- chalgham_presentation.pdf - 1.18MB
- chalgham_poster.pdf - 0.37MB
- chalgham_paper.pdf - 0.98MB
- chalgham_abstract.pdf - 0.31MB