The FEM simulation of the Surface Acoustic Wave Delay Line based on the P-matrix model for Sensor Application
Since the last few decades, the researchers are focused on new sensor material and novel design structure with high performances. Today various technologies are available but SAW sensors are preferable because of its characteristics such as low cost, low power, lightweight, rugged, simple fabrication and handling, small size, portability, wireless detection etc. The SAW sensors can be useful in a wide variety of applications including chemical and biosensors (enzyme, pathogens, Ebola, E. coli antigen detection), physical sensors (pressure, temperature, humidity, torque, strain etc.) and fluidics sensors. The SAW sensors have a frequency range from few MHz to GHz, therefore these sensors have significant frequency change for a small amount of mass loading. In this paper, the 2D-simulation of the surface acoustic wave on Lithium Niobate substrate based on the P-matrix model is presented. It is difficult to do SAW delay line simulation based on P-matrix model using FEM software since it requires tremendous memory and high performance of the computer, but COMSOL Multiphysics® 2D FEM package provides complete device simulation with comparatively low memory. The metallization is preferred as chrome and gold. The SAW sensors are presented with 3 different frequencies 17MHz, 20MHz and 50MHz. The Surface Acoustic Wave Gas Sensor module from the application library has been used as the reference for SAW delay line simulation. Three different modules have been used in COMSOL Multiphysics®, (i) solid mechanics module for mechanical acoustic wave propagation simulation (ii) electrostatics module for potential in interdigital fingers simulation and (iii) piezoelectric module for the conversion of electric energy applied in interdigital finger to mechanical acoustic energy simulation. The equivalent circuit of delay line also presented in this paper. The equivalent circuit of the SAW sensors is simulated in Quite Universal Circuit Simulator®. The presented approach shows good agreement between numerical simulation using MATLAB®, FEM simulation using COMSOL Multiphysics® and equivalent circuit simulated in Quite Universal Circuit Simulator®. The paper also discusses the meshing approach, flow chart for design the sensor, S parameter and Admittance characteristics of the SAW sensors.
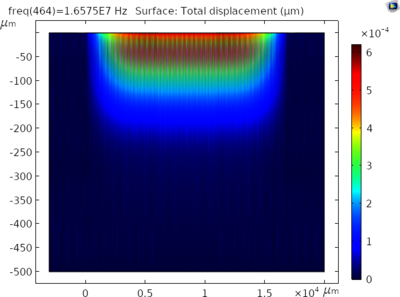