Efficiency of a Vertical Axis Wind Turbine (VAWT) with Airfoil Pitch Control
In this work, the CFD Module of COMSOL Multiphysics® software is used to study the efficiency of a Vertical Axis Wind Turbine (VAWT) with independently pivoting airfoils so that wind attack angles of these airfoils are adjustable. The work demonstrates how the efficiency of the VAWT is affected by the pivoting angles between individual airfoils and their support arms. The goal is to maximize energy production by controlling the pivoting pattern and thus the attack angles between wind and these airfoils when they are rotating with respect to the rotor shaft of the VAWT. As a type of wind turbine where the rotor shaft is placed vertically, VAWT is easier to install and maintain since the generator and clutch can be placed at the bottom of a VAWT where it is close to the ground. One additional benefit of this setup is that there is no need to point it into the wind. Despite these advantages, the VAWT type has been facing many challenges including low starting torque, low peak efficiency, narrow operating range, pulsatory torque, and dynamic stability problems. Researchers suggested pitch control systems such as the Self-Acting Stabilized Pitch Control and Aero Pitch for performance improvement. Experimental results have shown that these control methods result in improved starting torque, broader operating range and higher efficiency when compared to traditional fixed airfoil VAWT. Figure 1 shows the schematic of a VAWT system consisting of three airfoils that can pivot with respect to their own support arms. These arms are attached to the vertical central rotation axis of the rotor shaft of the VAWT via a hub at the top. Using individual actuators, pitch control of airfoils can be achieved by rotating the airfoils with respect to their own pivoting axis. For a given support arm position, such a pitch control of airfoils changes the angles between the airfoils and their support arms, which in turn changes the attack angles between wind and the airfoils causing redistribution of air pressure on surfaces of these airfoils. Consequently, at any given support arm positions, optimal pivot angles between the airfoils and their support arms for maximum torque exist. Therefore, an optimal airfoil pitch control pattern for individual airfoils for a complete round of rotation can be derived for maximum energy generation. The NACA 0012 airfoil as shown in Figure 2 is chosen for this study. As a first approach, a series of 2D models representing wind attack angles (thus airfoil pivot angles) ranging from 0 to 180 degree with 10 degree increment were created and simulated using the CFD Module of COMSOL Multiphysics® software. Figure 3 shows an example of such a model. By integrating the pressure vector along the surface of the airfoil, net force on the airfoil can be found. Torque and thus work can be derived by integrating along the airfoil surface the vector product between the vector from the central rotation axis of the rotor shaft to the airfoil surface and pressure vector.
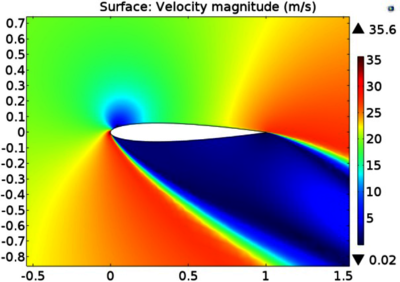
Download
- ma_presentation.pdf - 0.67MB
- ma_paper.pdf - 0.82MB
- ma_abstract.pdf - 0.11MB