Free Surface Deformation of the Weld Pool in Orbital Narrow Gap GTA Welding
Arc current welding is a widespread process in heavy industry for the assembly of metallic components. In order to ensure the good quality of assemblies welds, it is appropriate to master the welding process but also to have a deep understanding of interactions with the weld pool and resulting characteristics. During welding, material experiences a local phase change and exhibits a liquid/gas interface with the arc plasma. Then the weld pool is stretched under different effects such as arc pressure, surface tension or gravity. This latter has a significant impact once the welding torch rotates around the pipe or any other not flat welding position, affecting the weld shape dimensions. Here numerical simulation is used as a predictive in situ analysis tool which provides additional data to real-time measurements. It involves taking into account heat transfer and fluid flow inside the melt pool, but also electromagnetic phenomena induced by the electrical arc. For that purpose, a 3D steady-state model is implemented with energy, momentum, mass and current conservation equations. Marangoni effect, Lorentz forces and Buoyancy are also included. An additional set of equations deals with the deformation of the free surface due to driving forces and feed material. This is solved through a variational approach which minimizes the total energy of surface, coupled with an ALE moving mesh. Results are in good agreement with the state-of-the-art knowledge. By keeping constant welding parameters, the gravity impact on weld shape is discussed regarding three welding positions : flat position (PA), vertical up position (PF), vertical down position (PG). Early results are promising and shall be strengthened by a comparison between model outputs and experimental data from dedicated and instrumented mockups.
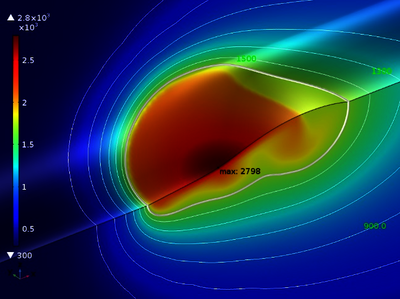
Download
- bruyère_presentation.pdf - 2.21MB
- bruyère_paper.pdf - 0.54MB
- bruyère_abstract.pdf - 0.22MB